

Now's the time to slip the small shrinky tube over the connector and the wire. Once you are crimped, the connector should look something like the last image. Honestly, I do this because I'm a bit obsessive. I then turn the connector 90 degrees and give it another light squeeze. Be careful not to completely crush the connector, you only want a light squeeze. I do this to make sure that the crimp is as tight as I can make it. I then put the connector into the next smaller anvil (26-28) and give it a light squeeze. Close the jaws completely to make sure that the crimp is good. The back of the connector should be wholly inside the jaws of the crimper with the non-crushing part wholly outside of the jaws. Next, the connector is placed in the jaws of the crimper (20-22) with the wings facing up (in the above picture, I have no idea how you are holding your crimper, so refer to the orientation above). If you don't then the wings are splayed out somewhat and the crimp can bend the fold-over wings the wrong way. The first thing that I do is to give the connector a quick and light nip in the crimper to close the housing a little. Your wires should now look something like the last image. If you wiggle it forward and back, it will put a lot of stress on the thin connection between the connector and the strip, you want it to do this so that it comes away easily, without resorting to cutting it with the side-cutters. Take the piece out of the alligator clip and carefully wiggle the strip back and forth to take it off. You don't need to add any more solder to make the joint good. When the solder is hot, it will flow up the wire by capillary action. Next, position the wire inside the U channel of the Dupont connector so that the beveled PVC is between the fold-over wings.Īpply your soldering iron to the blob of solder that you soldered in earlier. Use a reasonable blob of solder (leaving a blob of about 3mm) so that soldering in the wire is EASY. That is, between the fold-over wings of the connector and down to the handy little line in the connector body. You need to tin the inside of the connector where the wire will go. With the connector in an alligator clip on your Third Hand (or stuck in some plasticine for stability). It is much easier to manipulate and much easier to solder when you leave the connector strip on board. Once you get the hang of it, you will find it easy and rewarding.Ĭut two connectors from the strip, leaving them on the strip. I've made dozens of connector wires so far, for connecting a 9V snap to a PCB, connecting LED to a pin header, connecting sub-boards and for making USB power cables. The Dupont housing doesn't care if the connector is male or female. You'll need some decent wire cutters (mine cost about $16) and crimping pliers for Dupont connectors (mine cost about $12) The Dupont connectors (Female gold plated 2.54mm) for $10 for a packet of 200, Male (not gold, 2.54mm) for $7.90 for a packet of 200 ($0.04 each)ĭupont housing (1P F2.54mm pitch) for $2.86 for a packet of 100 ($0.03 each) The Dupont housing (2P F2.55mm pitch) for $4.75 for a packet of 200 ($0.05 each) I've bought wire for as low as $8 for a 10m roll (stranded copper in pvc sheath)

The cost is pretty fair, when you tote it all up:
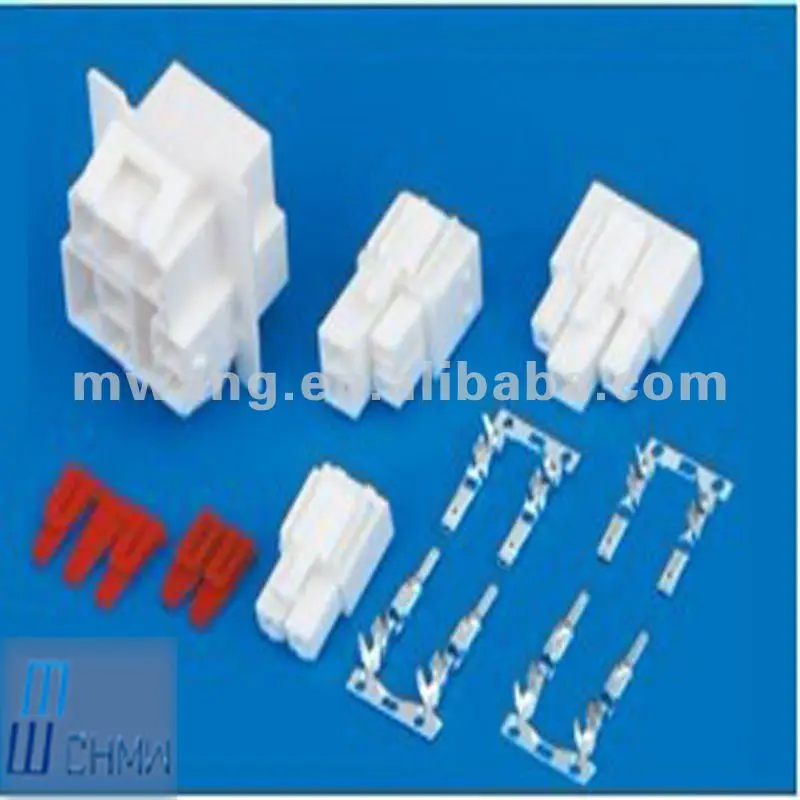
#Pin housing connector free#
Making your own connecting wires means that you are free of the tyranny of the length and colour of connectors/jumpers that you need to buy, it is MUCH cheaper and you are never going to be short of a connector/wire again (of course, you still need wire, the connectors and the connector housing). One of the things that you can do yourself (and pretty cheaply) is to make your own connecting wires.
